Function-oriented approach – modular manufacturing in the automotive industry
The most important facts in brief
- The automotive industry is in a state of upheaval
- Future topics such as alternative drives, digitalization and autonomous driving are pushing OEMs to rethink their approach
- This also affects production and its cycle specifications for assembly
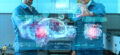
The competition for the leading role in electromobility and the future topics of digitization and automated driving are the drivers for a wide range of process changes. Here, for example, climate targets and regulatory requirements play a strong role – but the changed behavior of customers is also forcing manufacturers to transform themselves.
However, transformation here does not just mean the development of new forms of drive or further innovations on the vehicle. The transformation in the automotive industry affects not only the research departments of the car manufacturers, but also the production lines. The changed requirements present the production of the major OEMs in particular with the challenge of becoming even more efficient and, above all, faster. Cycle times in assembly, for example, must be drastically reduced. As a result, modular production is becoming even more of a focus. In addition to the OEMs, this particularly affects tier 1 suppliers who deliver directly to the manufacturers.
Increase in cycle times in the automotive industry
OEMs have always tried to maximize efficiency in manufacturing and generate maximum output with tight cycle times and just-in-time & just-in-sequence production. Currently, however, there is a challenging key figure that has ushered in a new era: The 10-hour mark for the complete assembly of a vehicle. This mark has already been broken and has since been regarded as a target for the entire industry to strive for.
This objective poses a major challenge for automakers. Currently, most OEMs need well over 25 hours to completely assemble a vehicle. The leap below 10 hours can only be achieved with a completely rethought production concept. To achieve this, OEMs will have to rely on module assembly in the future and also involve component manufacturers and tiers more closely in the assembly and development process.
Modular production of component manufacturers
This is where the function-oriented approach comes into play. The OEMs define only the function of the application and hand over various development and assembly activities to the component manufacturers. This means that the pre-assembled modules only have to be delivered to the OEM’s production facility and mounted on the body. Many time-consuming assembly steps are thus shifted from the OEM to the component manufacturers.
This means that in the future product development will also be partly the responsibility of the supplier companies, which will thus increasingly also become development specialists. Component manufacturers will therefore be able to supply complete solutions for optimized, lean production independently in the future. This will ease the burden on automakers and give them the necessary freedom to focus on global and forward-looking issues such as new mobility concepts.
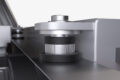
WITOL joining technology for optimized assembly
In this new manufacturing concept, precisely fitting connections are central to optimize assembly. This is where WITOL’s competences come into play. With its intelligent fastening systems and the possibility to develop 100% customized solutions, WITOL acts as an engineering partner between OEMs and component suppliers. By using WITOL tolerance compensation elements, not only precise gap dimensions between adjacent components are achieved. Rather, the WITOLs allow a stress-free component connection and thus contribute to a high-quality appearance in the end product.
In addition, the WITOL tolerance compensation systems simplify the entire assembly process, which is particularly advantageous when joining modules that will become increasingly complex in the future. Thus, the WITOLs can already be pre-assembled on the individual modules and ensure the highest precision in the bolting process. By simplifying the entire joining process, cycle times can be sustainably optimized. Even the smallest deviations at the screwdriving points with tolerances are reliably compensated for, eliminating the need for time-consuming corrective measures or reworking.
Conclusion
New solutions for the automotive production
The transformation of the automotive industry has been progressing dramatically in recent years. User behavior and demands are changing dramatically, affecting not only vehicle research and development but also automotive production processes. The increased focus on maximally efficient production is creating a need for repositioning both among automotive manufacturers and, in particular, among suppliers.
There are already approaches to tackling these challenges in the automotive industry. One trend will become the modular and function-oriented development approach, in which large modules already pre-assembled to the maximum are mounted on the body-in-white. Here, joining technology is the key to optimized manufacturing processes. Here, WITOL’s tolerance compensation elements ensure optimized cycle times and simplified final assembly. In addition, the joint gaps are reliably compensated – for the highest quality in the end product.